I really love electronics and all the challenges that come with solving problems and inventing things that have never existed before but building prototypes–especially of PCBs designed for manufacturability with tiny ICs and passives: ugh!
It was fine when I was making basic circuits, but hundreds of tiny pieces, painstakingly placed one by one… Life is too short for the drudgery.
I just couldn’t bring myself to send thousands of dollars to China for a cheap mystery machine and I have neither the space nor the budget for something seriously industrial.
I kept thinking how “there are a zillion 3d printers, now, how hard could it be to adapt something to do pick&place?”.
Turns out, it’s pretty hard. But the work has been done for us by Juha Kuusama. He has created and released the LitePlacer.
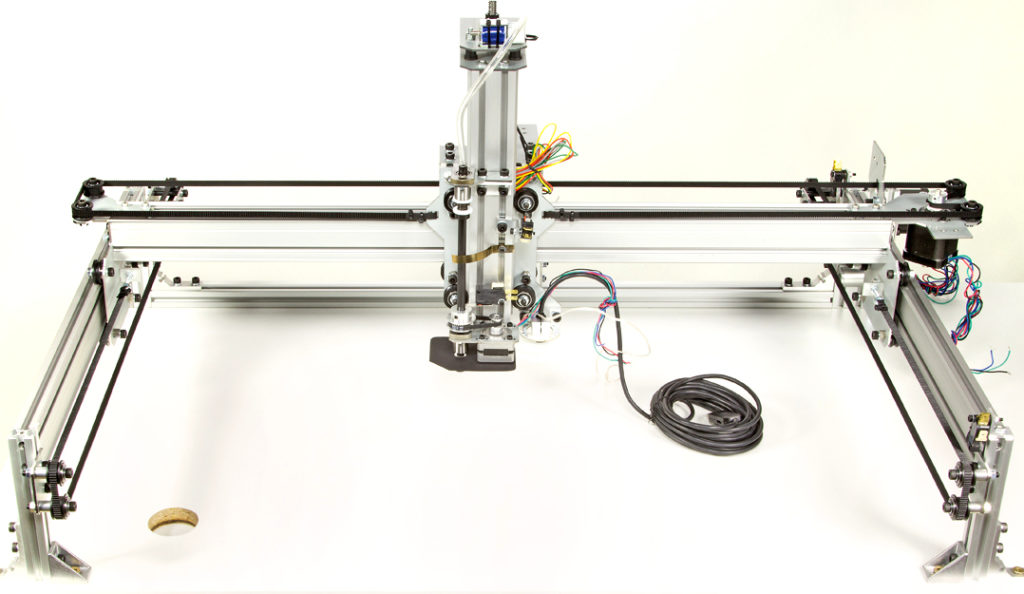
Its main advantages, to me, are:
- it’s based on standard hardware (e.g. aluminum extrusions, steppers etc);
- it’s open: open source software, open hardware;
- it has down and up cameras, and can use vision processing to locate fiducials and component feeds;
- you can get a kit with all the goodies in one go;
- it has its own software and can apparently be used with OpenPnP as well; and
- you build it yourself
Ok, that last one is a bit iffy, in terms of being an advantage. But if you’re reading this, you are a maker and you know the satisfaction to having made something and that’s already cool but, more importantly, I’m hoping going through the process will make me intimately familiar with every part of the system.
I want to be able to do something should something go wrong. I want to be able to know how it works and adjust or enhance it. That won’t work with a Chinese black box PnP.
I’ll be documenting the process and creating videos along the way. I just published the first, which goes over the stuff you’ll need in addition to the kit. Check it out: